Flexible electronic technology in development
Flexible electronic technology is an emerging scientific technology. Due to its unique flexibility and ductility, flexible electronic technology has broad application prospects in many aspects.
Flexible Electronics (Flexible Electronics), also known as Plastic Electronics, Printed Electronics, Organic Electronics, Polymer Electronics, etc .; is the production of organic / inorganic materials electronic devices in flexible / Emerging electronic technology on ductile plastic or thin metal substrates.
In the impression of people, organic materials, such as plastics, are good insulators, and few people think that plastics can also conduct electricity. In recent years, due to new breakthroughs in the research of conductive polymers, organic materials can be changed from traditional insulators to conductive semiconductors, and flexible electronics have emerged. The development of modern chemistry and other technologies has promoted the development of a discipline such as flexible electronics. The key to flexible electronics manufacturing includes manufacturing processes, substrates, and materials. Its core is micro- and nanopatterning (Micro- and Nanopatterning) manufacturing, which involves interdisciplinary research in machinery, materials, physics, chemistry, and electronics.
With its unique flexibility / ductility and efficient and low-cost manufacturing process, flexible electronics has wide application prospects in the fields of information, energy, medical and defense, such as flexible electronic displays, organic light-emitting diodes OLED, printed radio frequency identification (RFID), Thin-film solar panels, electronic newspapers, and electronic patches (Skin Patches) / artificial muscles, etc.
In addition to integrating technologies in the fields of electronic circuits, electronic components, materials, flat display and nanotechnology, flexible electronics also spans industries such as semiconductors, packaging and testing, materials, chemicals, printed circuit boards and display panels to assist traditional industries, such as The transformation of industries such as plastics, printing, chemicals and metal materials has increased the added value of the industry. Therefore, the development of flexible electronic technology will bring revolutionary changes to the industrial structure and human life.
Flexible electronic technology is a brand-new electronic technology revolution, which has aroused widespread attention all over the world and developed rapidly. The United States “Science” magazine listed organic electronic technology progress as one of the world’s top ten scientific and technological achievements in 2000, juxtaposed with human genome sketches, cloning technology and other major discoveries. The American scientists Alan Hager, Alan Mark Dillmead and the Japanese scientist Hideki Shirakawa won the 2000 Nobel Prize in Chemistry for their pioneering work in the field of conductive polymers.
The difference between flexible electronics and traditional electronics manufacturing
At present, the electronics industry basically belongs to the traditional semiconductor industry. The equipment used in manufacturing is quite large, and the cost is high, and the manufacturing efficiency is low; the concept of the entire flexible electronics is to print traditional semiconductor products, components, and circuits by printing. Substitute. The difference between flexible electronics and traditional electronic circuits is mainly viewed from three aspects:
(1) Application prospects
Once a very soft substrate is used in design or the circuit is made invisible or foldable, it is very different from the traditional rigid substrate.
(2) Manufacturing cost
Flexible electronics use a roll-to-roll printing process, and the use of materials can also avoid the problem of wasting more than 95% of materials like photolithography. The area printed by printing is equivalent to the area used, and its usage rate is More than 90%, from a long-term development perspective, the printing method will be much lower than the cost of traditional lithography technology; silicon CMOS wafers generally cost $ 10 per square centimeter, composite semiconductors are even more expensive, and the ideal cost for flexible electronics is At 0.1 US dollars per square centimeter, the huge advantages of flexible electronics can be seen from the cost.
(3) Investment perspective
Traditional semiconductor factories constantly require billions or even tens of billions of investment, but flexible electronic printing is like traditional printing. As long as the investment is tens of millions, the basic scale can be established. It should be emphasized that the ink used for printing is different from traditional printing and requires special development. The initial cost of development is relatively high due to the small amount, but the cost will become lower after mass production.
Structure and material of flexible electronic system
Although flexible electronic technology can be applied in different fields, its basic structure is similar, including at least the following four parts: electronic components, flexible substrate (flexible substrate), cross-linked conductor (finterconnect) and adhesive layer.
Flexible electronic system structure
1. Electronic Components
Electronic components are the basic components of flexible electronic products, including thin-film transistors and sensors commonly used in electronic technology. These electronic components are not fundamentally different from those of traditional electronic technology. Some components use inorganic semiconductor materials (such as silicon). Because their materials are relatively brittle, they are prone to brittle fracture during deformation, so they are usually not directly distributed in the circuit. On the board, it is first placed on a rigid micro-cell island (cell island), and then the micro-cell island carrying components is then distributed on the flexible substrate. The advantage of this is that it is beneficial to protect electronic components and avoid their Damaged during bending. Of course, some electronic components can also be directly distributed on the flexible substrate, for example, some thin film transistors, due to their own characteristics, can directly withstand a certain strain without affecting its function.
Compared with traditional microelectronics technology, the use of organic electronic components is a significant feature in flexible electronic technology. Organic thin film transistors occupy a very important position. The use of organic materials is to reduce the weight and thickness of components. Increasing its flexibility and ductility creates conditions.
2. Flexible substrate
Flexible substrate is the most prominent place where flexible electronic technology is different from traditional electronic technology. It has the common characteristics of traditional rigid substrates, the first is insulation: the insulated flexible substrate ensures that electronic equipment will not leak during use, not only to ensure that it can work normally, but also to ensure the safety of its use. The second is higher strength: no matter what kind of electronic technology, the role of the substrate is equivalent to the role of the skeleton, without higher strength as a guarantee, it can not guarantee its normal use.
Once again, it is cheap: the substrate material is one of the most used materials in the circuit, and only the use of inexpensive materials can effectively reduce the cost of electronic products.
In addition to the common characteristics of the above substrates, flexible substrates also have their own unique characteristics. The first is flexibility: the flexibility of the flexible electronic system is mainly manifested through the substrate, and products with different requirements for flexibility can use substrates of different materials; for example, electronic skin usually uses a very flexible silicone organic resin (Si1icone), while the flexibility Electronic displays have weaker requirements for flexibility than electronic skins. Polyethylene terephthalate (PET) is commonly used as polyester.
Secondly, it is thin film: although it is called a substrate, it is no longer a “board” in size, but a thin film; the substrate of a flexible electronic system is usually about 1 mm, which reduces the cost of materials and the product. weight.
In view of the above considerations, the use of high molecular polymers for flexible substrates is an ideal choice. Currently available flexible substrate materials include DuPont ’s Kapton polyimide (PI) film materials, polydimethylsiloxane, polyethylene terephthalate (PET), etc. It can well meet the requirements of insulation, flexibility and strength.
3. Cross-linked conductor
Electronic components are first distributed on rigid microcell islands. Many such microcell islands are then distributed on the flexible substrate. These microcell islands do not exist independently, they are connected by cross-linked conductors A complete flexible circuit, that is to say, the cross-linked electrical conductor acts as a wire in a flexible electronic system. The cross-linked conductor is attached to the flexible substrate in the form of a metal film.
4. Adhesive layer
The bonding of various components of the flexible electronic system requires an adhesive layer, and the adhesive layer is particularly important for the combination of the cross-linked conductor and the flexible substrate. The adhesive layer of the flexible electronic system should have the following characteristics:
(1) Heat resistance. During the assembly and use of flexible electronic products, it is inevitable to experience an environment above normal temperature, and certain heat resistance is necessary.
(2) Binding force. Because flexible electronic products are constantly subjected to tension, compression and bending deformation during use, the two thin layers connected by the adhesive layer usually have different mechanical properties. If the bonding force is not large enough, it will inevitably cause the relative sliding of the two thin layers or even Peel off.
(3) Bending ability. The adhesive layer itself is an integral part of the structure of a flexible electronic system, and its own bending ability has an important influence on the bending ability of the entire structure. At present, the commonly used adhesive layer materials in flexible circuits mainly include acrylic resin and epoxy resin.
5. Overlay
The cover layer (also called encapsulation layer) mainly protects the flexible circuit from dust, moisture or chemicals, and can also reduce the strain on the circuit during bending, and recent studies have shown that the cover layer can reduce the flexibility of the circuit The stress intensity at the edge of the rigid microcell island (fcellisland) can suppress its delamination from the flexible substrate.
According to the characteristics of flexible electronic systems, the cover layer needs to be able to withstand long-term deflection, so the cover layer material and the substrate material, fatigue resistance must meet certain requirements. In addition, the cover layer covers the sub-etched circuit, so it is required to have good conformability to meet the requirements of bubble-free lamination. Common materials used for the cover layer are acrylic resin, epoxy resin and polyimide.
Manufacturing process of flexible electronic system
Like traditional IC technology, manufacturing processes and equipment are also the main driving forces for the development of flexible electronic technology. The technical level indicators of flexible electronics manufacturing include chip feature size and substrate area. The key is how to manufacture flexible electronic devices with smaller feature sizes on larger format substrates at lower cost.
The flexible electronics manufacturing process usually includes: material preparation → deposition → patterning → packaging, which can be integrated by roll-to-roll (R2R) substrate transport.
Flexible electronic manufacturing mainly focuses on factors such as production cost, production efficiency and achievable feature size, and compatibility of organic materials. In recent years, due to the breakthrough of active materials and its patterning technology, flexible electronics manufacturing technology has made great progress.
The core of flexible electronics manufacturing is thin film transistor (TFT) manufacturing. Its key manufacturing technology is to make high-resolution patterning technology of channel length between source and drain, which directly affects device performance such as output current and switching speed. In the organic semiconductor patterning process, it is particularly necessary to eliminate parasitic leakage and reduce crosstalk to ensure a high switching ratio. Most applications require an organic thin film transistor (OTFT) channel length of less than 10 microns. Existing patterning technologies include photolithography, shadow masks, and printing (microcontact printing and jet printing).
Energy beam technologies such as photolithography are widely used in the patterning of microelectronic devices with high resolution. However, due to their complicated process, expensive equipment, and solvents and developers cannot be used for plastic substrates, plus time-consuming materials, only suitable Small-area patterning requires severe environmental requirements when etching the bottom layer. When removing photoresist, it will destroy the activity of organic electronic materials and polymer substrates. It is limited in flexible electronic manufacturing applications.
Shadow mask technology is a “dry” process, which can prevent solvents from damaging organic semiconductors, but the resolution is limited.
Printing technology realizes functional material deposition and patterning in the same step, the main methods are: (1) transfer and paste the complete circuit to the flexible substrate, such as transfer printing (stamp); (2) directly on the flexible substrate Preparation of circuits, such as jet printing and micro-contact printing (soft etching).
In the traditional printing method, the entire structure is first prepared on a silicon wafer or glass plate by standard photolithography methods, and then transferred to a flexible substrate to manufacture a high-performance device. Due to the application of photolithography and high-temperature deposition technology, the transfer printing technology can only manufacture small-area devices, and the processing cost is high.
Micro-contact printing can produce multi-level patterns for masks, which can be integrated with R2R batch manufacturing technology. Usually a master can produce more than 100 stamps, and each stamp can achieve more than 3000 stamps. The cost of the stamp is relatively low. A 60nm high-resolution pattern can be produced at a speed of several centimeters per second, but a multilayer pattern is realized more difficult. Micro-contact printing can be used for a variety of materials such as amorphous silicon, polysilicon and TMOS, but it is difficult to directly etch organic materials. Lan Hongbo et al. Made a detailed discussion and analysis on the research progress and development trend of nano-imprint etching mold technology.
The ideal patterning process of flexible electronics should meet: low cost, large area, batch process, low temperature, “plus” type, non-contact, real-time adjustment, three-dimensional structure, easy multi-layer registration, printable organic / inorganic Materials etc. Jet printing is a non-contact, non-pressure, and non-plate printing and copying technology. It has the characteristics of plateless digital printing. The solution is written directly at room temperature to achieve digital flexible printing, which simplifies the manufacturing process. Using solutionized semiconductor and metal materials to replace traditional vacuum deposition materials can effectively reduce costs. Jet printing also has the following advantages:
(1) The quality of the pattern is not limited by the focal length of the lithography, and it can be patterned on non-planar surfaces or even deep trench structures;
(2) Good compatibility with organic / inorganic materials;
(3) Direct use of CAD / CAM data processing devices can realize large-area dynamic alignment and real-time adjustment;
(4) As a non-contact patterning technology, it can effectively reduce defects, and can use virtual masks to compensate for defects such as deformation and misalignment between layers;
(5) Print-on-demand (DOD) technology without physical mask;
(6) The rapid design and processing of complex three-dimensional microstructures can be realized, and the graphics can be quickly changed through the software-based printing control system.
Application of flexible electronics
With the development of flexible electronic technology, various electronic products came into being. Just as microelectronic technology provides a technology platform for large-scale integrated circuits and computer chip technology, flexible electronic technology provides a brand-new technology platform for the research and development of new products. Flexible electronic products are currently in the initial stage of research and development, and some products have been put on the market. From the current research and development trends, flexible electronic technology has a wide range of applications in the following three areas.
1. Flexible Electronic Display
Flexible electronic display (flexible electronic display) is a brand new product developed on the flexible electronic technology platform. Unlike traditional flat panel displays, this type of display can be bent and folded repeatedly, thus bringing great convenience to our lives.
For example, all visual materials, including various books, newspapers, magazines, and video files can be presented on this display and can be viewed anytime, anywhere. Although such as MP4 players and personal digital assistants (PDAs) can also meet such usage needs, the display screen cannot be bent or folded, and can only read and watch these texts and videos within a small screen , The visual effect is greatly restricted. In comparison, the flexible electronic display has unparalleled advantages. It is like a newspaper. When needed, it is unfolded, and after use, it is curled or even folded, ensuring the convenience of carrying and taking full account of the visual effects.
It is worth mentioning that flexible electronic displays use more lightweight organic materials instead of inorganic materials, so their weight is lighter than traditional displays, and this feature is conducive to improving their portability. In addition, the use of high-molecular organic materials offers the possibility of reducing costs. In addition, the flexible electronic display has the characteristic of thin thickness, and its thickness can be much smaller than that of the currently popular liquid crystal display, so another name of the flexible electronic display is paper-like electronic display.
2. Thin-film solar panels
Thin film solar cell (thin film solar cell) is another specific application of flexible electronic technology. In today’s world, energy has become a topic of global concern, and China is not only facing energy shortages, but also environmental pollution. Solar energy, as a kind of clean energy, can effectively ease the contradiction of energy shortage on the premise of zero environmental pollution.
As the most commonly used way of using solar energy, solar panels can cover a large area at the lowest cost to effectively use solar energy. At present, amorphous silicon thin-film solar panels have been successfully developed and entered the market.
Thin-film solar panels based on flexible electronic technology can meet the needs of high-power generation. For example, such thin-film solar panels can be used in solar power plants in sunny desert areas.
In addition to this, it can also take full advantage of its flexibility and lightness, and integrate it on clothes. Wear this kind of clothes to walk or exercise in the sun, and the power of small electrical appliances (such as MP3 players and notebook computers) that can be carried with you can be supplied by the thin-film solar panels on the clothes, thereby achieving the purpose of saving and environmental protection.
3. The application background of flexible electronics in the field of RFID
Radio frequency identification (RFID) technology has the characteristics of complete information input and processing without manual contact, fast and convenient operation, rapid development, etc. It is widely used in production, logistics, transportation, medical treatment, food and anti-counterfeiting fields. Radio frequency identification systems are usually composed of transponders and readers.
The electronic tag is one of many forms of transponders. It can be understood as a transponder with a film structure, which has the characteristics of convenient use, small size, light and thin, and can be embedded in products. In the future, more and more electronic tags will be used in radio frequency identification systems.
The structure of electronic tags is developing in the direction of light, thin, small and soft. In this respect, flexible electronic devices have unmatched advantages over other materials. Therefore, the future development of RFID electronic tags is likely to be combined with flexible electronic manufacturing, making the use of RFID electronic tags more widespread and convenient. In addition, it can greatly reduce costs and bring higher benefits. This is also one of the future development directions of flexible electronics manufacturing.
Making low-cost flexible electronic tags has two meanings. On the one hand, it is a useful attempt to make flexible electronic devices. Electronic circuits and electronic devices are developing in the direction of “light, thin, small, and soft”, and the development and research of flexible electronic circuits and electronic devices are more noticeable.
For example, the flexible circuit board that can be produced now is a circuit that contains delicate wires and is made of a thin, pliable polymer film. It can be applied to surface mounting technology and can be bent into countless desired shapes.
The flexible circuit using SMT technology is very thin, lightweight, and the insulation thickness is less than 25 microns. This flexible circuit can be bent arbitrarily and can be bent into a cylinder to make full use of the three-dimensional volume.
It breaks the traditional mindset of the inherent use area, thereby forming the ability to make full use of the volume shape, which can greatly increase the effective use density in the current method and form a high-density assembly form. Compliant with the development trend of “flexibility” of electronic products.
On the other hand, it can accelerate the process of recognition and development of radio frequency identification technology in China. In radio frequency identification systems, transponders are the key technology. Electronic tags are one of many forms of RFID transponders, and flexible electronic tags are more suitable for more occasions. The reduction in the cost of electronic tags will greatly promote the real wide application of radio frequency identification technology.
4. Electronic skin
Another important application of flexible electronic technology is electronic skin. Electronic skin is also called skin-like electronics. Its basic feature is to integrate various electronic components on a flexible substrate to form a skin-like circuit board. It has high flexibility and elasticity like skin, and can be used in many other electrical equipment.
For example, electronic skin can be widely used in robot technology: electronic skin integrates various sensors and electrical conductors, converts the external force or heat into electrical signals, and then transmits them to the robot ’s computer for signal processing. Therefore, electronic skin Called sensitive skin.
The two most basic features of electronic skin can be summarized as:
(1) It is flexible and elastic like human skin so that the robot can act flexibly and agile like a real person.
(2) Sensors are distributed on the electronic skin so that the robot can perceive the changes of the external environment keenly.
At present, research on electronic skin at home and abroad is booming. Aiming at the important electronic component of the robot skin, the sensor, China has made some progress in its principle and application research. The design method of electronic skin based on infrared sensors improves the robot’s ability to perceive the unknown environment in order to avoid obstacles in time.
In addition, the signal fusion problem of many sensors in the electronic skin is solved. Because the PVDF piezoelectric film has the characteristics of high piezoelectric capacity, flexibility, extremely thin and light weight, which is very close to the characteristics of human skin, research on electronic skin sensors around this material at home and abroad is relatively common.
Foreign countries have also made considerable progress in the research of electronic skin related issues. Researchers in Japan not only developed relevant theories of electronic skin, but also made experimental products. To study the force perception of electronic skin, the possibility of force sensing is discussed by establishing the relationship between force and sensor capacitance.
Although the basic principle of electronic skin is not complicated, how to cover the robot with electronic skin is quite challenging, because electronic skin is to feel the external environment of the robot’s whole body, and it must be integrated. At the same time, as an external component, the electronic skin may be damaged by external factors. When the whole or part of the electronic skin is damaged, it needs to be replaced in time.
Aiming at this demand of electronic skin, the concept of electronic skin unit module is proposed, and each unit module is connected through a serial bus, thereby achieving the unity and integrity of electronic skin. However, the use of electric wires inevitably increases the weight of the electronic skin, and the insulating rubber layer of the electric wires also restricts the flexibility of the electronic skin to a certain extent.
Under this circumstance, an in-depth study has been made on the connection conductor of the electronic skin, and a new technology is proposed in which a metal (gold) film is attached to pre-stretched polyethylene terephthalate, commonly known as a polyester substrate. Experiments have shown that this metal film can still conduct electricity even when the tensile deformation is doubled (ie, the strain reaches 100%).
Research on electronic skin sensors is currently focused on the sensing of a single external information (such as force). However, as an electronic skin, it is very important to sense multiple external information, that is, you can feel external stimuli such as force, temperature, and humidity at the same time. To achieve this goal, at least three technological breakthroughs need to be achieved:
(1) Material selection: The realization of the sensor sensing function depends to some extent on the functional characteristics of the sensor material, such as piezoelectricity, pyroelectricity or semiconductivity, so the research and application of functional materials affect the sensor technology development of.
(2) Processing of multiple sensitive signals: a complete (robot) electronic skin has collected a considerable number of sensory microelements, each of which has the function of responding to the external environment, and in some cases each sensory The micro element also has to respond to multiple signals (such as simultaneous susceptibility and heat). In the case of a very large amount of signal, how to process the signal and determine the countermeasures of the robot’s stimulation to the outside world is an important issue.
(3) Optimization of mechanical properties of electronic skin: As an important application of flexible electronic technology, electronic skin must meet the realization of flexibility under the guarantee of strength; the optimal design of the lightest quality without premature damage is also an important content to be considered.
In addition to robots, electronic skins can also be used in artificial organs, such as the artificial heart used to treat heart disease. Of course, this places more stringent requirements on the materials of electronic skins. In short, the electronic skin has fully exerted the characteristics of light and flexible structure of the flexible electronic system, and has wide application prospects.
With the development of flexible electronic technology, various electronic products came into being. Just as microelectronic technology provides a technology platform for large-scale integrated circuits and computer chip technology, flexible electronic technology provides a brand-new technology platform for the research and development of new products.
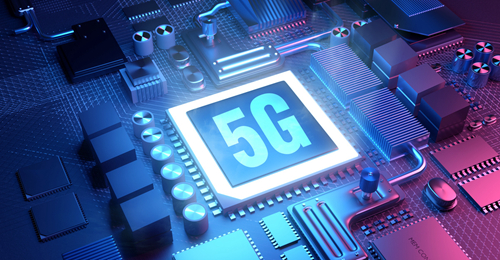
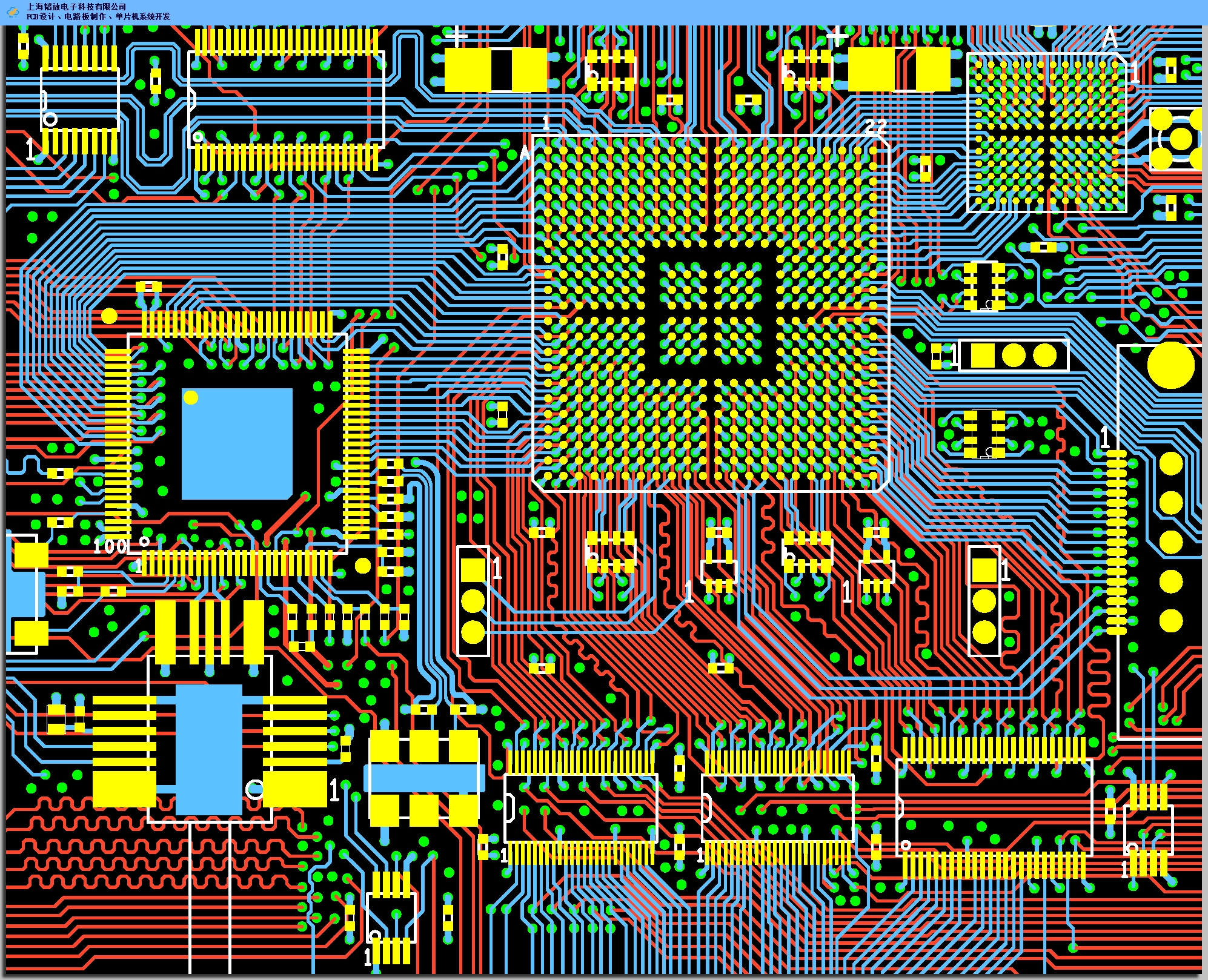
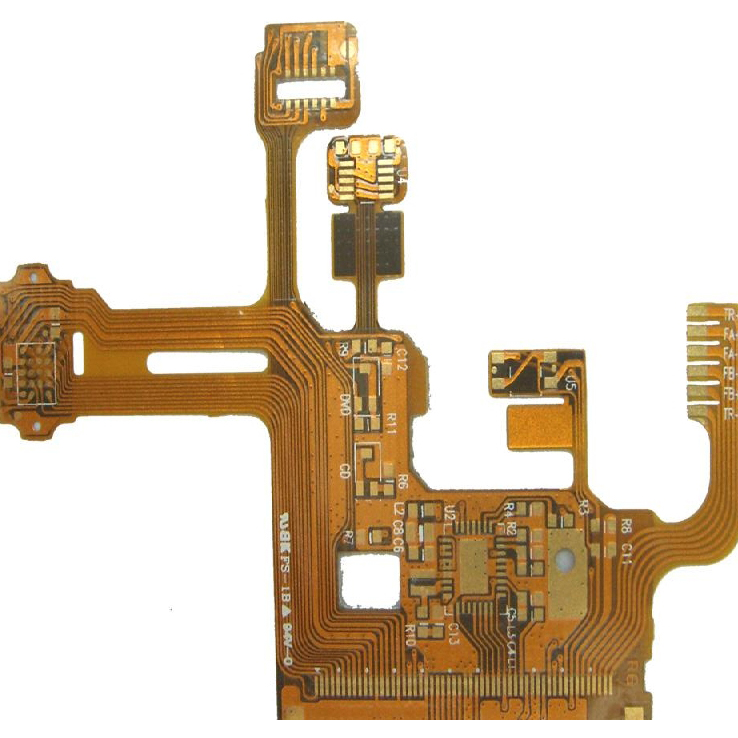
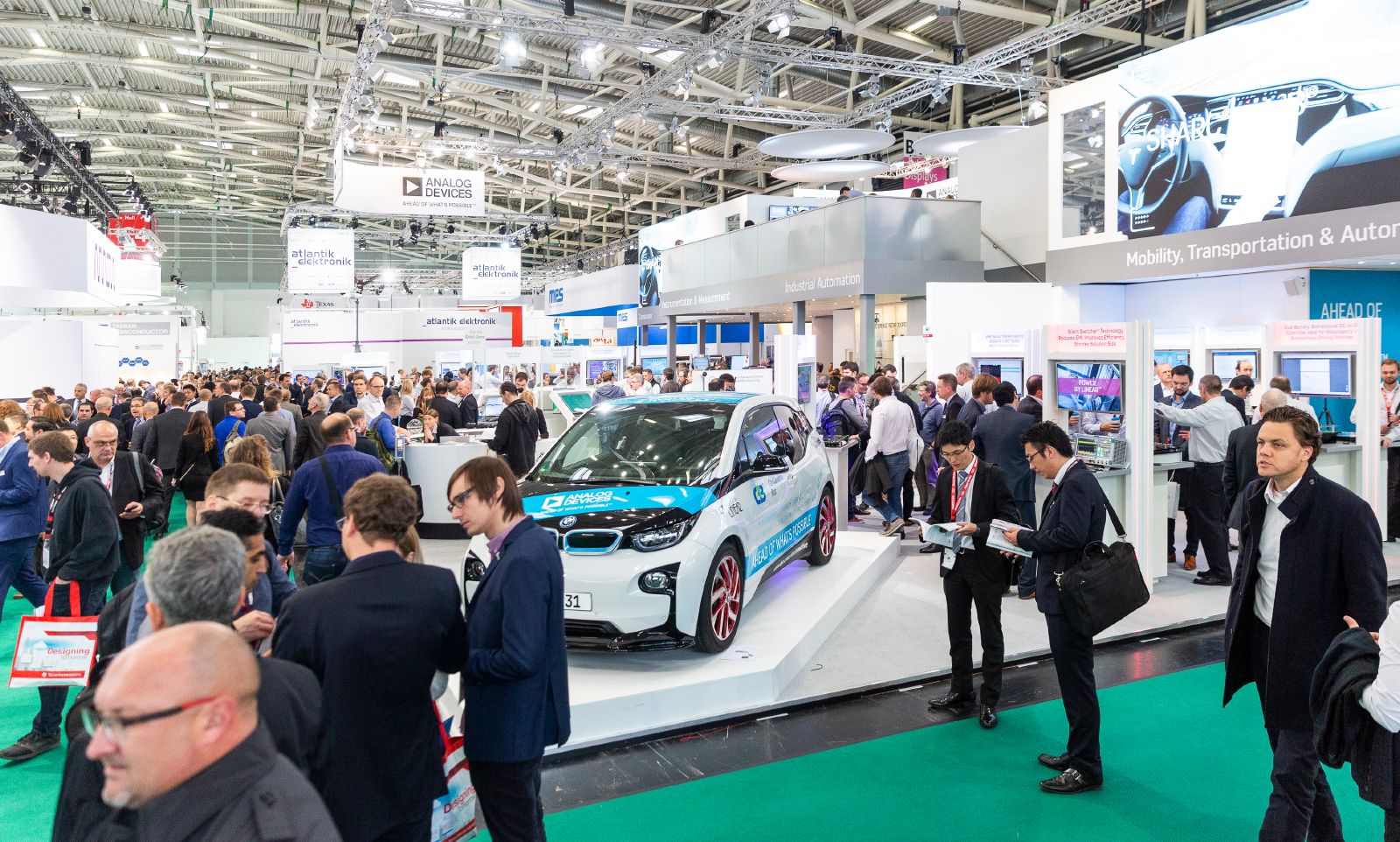